The ups and downs of anodized metals
By Renée Newman
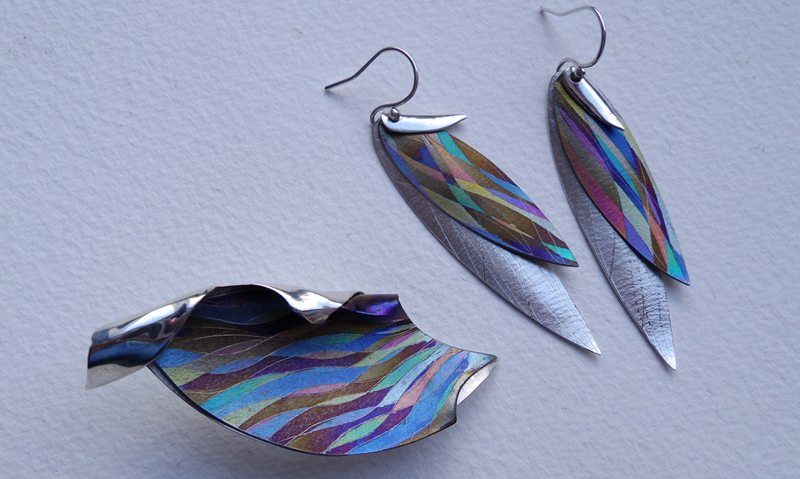
Photo by Brian Eburah
Did you know it is possible to create permanent colours and designs on metal without heat, plating, enameling, or caustic chemicals (Figure 1)? This can be done on reactive metals, such as titanium and niobium, by running a controlled electric current through them while the metal is dipped in soapy water or touched with a wet sponge/wet brush. This is an electrolytic process called ‘anodizing.’
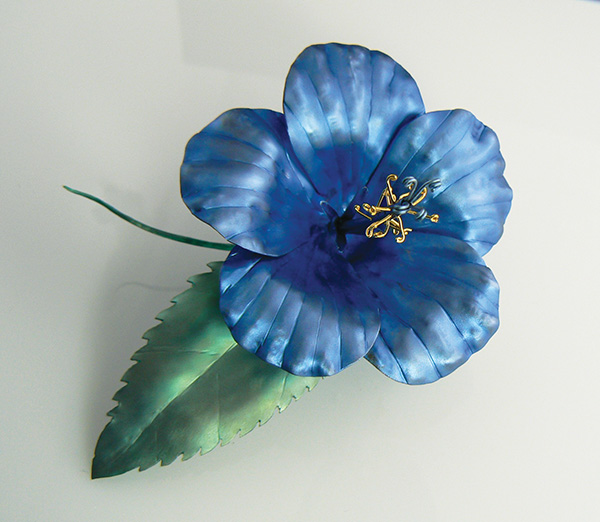
Photo courtesy Oscar Art Jewelry
During this process, the controlled current creates a transparent oxide film on the metal’s surface, which causes light interference as it is reflected from both the surface of the oxide and the surface of the metal. The appearance of colour perceived by the eye is determined by the thickness of the layer and the surface finish. The voltage used determines the thickness of the oxide deposit and the apparent colour obtained. Browns require the least voltage (about 10 to 15 volts) and greens the most (85 to 90 volts). Since the colours are created by light interference and not dyes, they resemble those seen in soap bubbles or oil floating on water—as such, one should not expect to see black, red, or dark orange colouring on metal that is only anodized. It is possible, however, to create charcoal-black niobium by heating it red hot.
Other reactive metals (including tantalum, aluminum, and zirconium) can also be coloured by anodizing; however, because titanium and niobium are more accessible and used more often for jewellery, these materials are the focus of this article. Anodizing aluminum is, indeed, a more complicated process—one which involves heating and chemicals in addition to an electric current. Anodized aluminum is evenly coloured and cannot achieve the rainbow-type hues seen in anodized niobium and titanium.
Titanium and niobium are produced commercially, which means initial ingots will weigh in excess of 10,000 lbs. The individual wrought products are made in small quantities and sold by the pound or kilo. (To simplify the purchase process, the product may be sold by the square inch and foot to individuals.)
Niobium
Niobium (Nb) is a lustrous and malleable grey metal, noted for the beautiful colours it can obtain during anodizing (Figures 2 & 3). It was discovered in 1801 by the English chemist Charles Hatchett, who named it ‘columbium.’
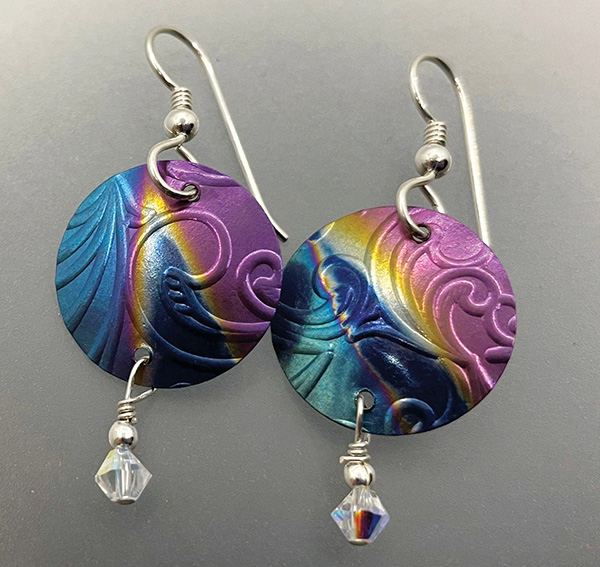
Photo by Jana Cooper
Forty years later, the metal was rediscovered by the German chemist Hienrich Rose. He named it ‘niobium,’ after Niobe, the daughter of the Greek mythological Tantalus because niobium is closely related to the metal tantalum. It wasn’t until 1950 when the name ‘niobium’ was officially adopted by the International Union of Pure and Applied Chemistry (IUPAC).
Brazil is the leading producer of niobium, though Québec is another important producer. The Niobec mine, located in Saint-Honoré, produces about eight to 10 per cent of the world’s niobium and is the only underground niobium mine.
The metal has a variety of uses beyond jewellery making. Niobium strengthens steel and is important for jet engine components and the nuclear industries. It is also added to glass to give the material a higher refractive index, and allow the optical industry to make thinner corrective lenses. Niobium is also used in pacemakers, as well as for superconducting magnets in MRI scanners.
Titanium
People looking for sturdy, comfortable jewellery are attracted to titanium (Figures 4 & 5). Indeed, the same exceptional strength and light weight that makes this metal ideal for the aerospace industry is also useful for rings and watches, as these pieces must be able to withstand a lot of wear.
Titanium (Ti) was first discovered in 1791, but wasn’t commercially available until the 1940s when its refining process was invented by William J. Kroll. It has been used for jewellery since the 1970s and has become increasingly popular—not only as an anodized metal, but as an alternative grey metal as well.
Bill Seeley, president of Reactive Metals Studio, Inc., and creator of the YouTube video titled, ‘How to Anodize Reactive Metals: Coloring Niobium and Titanium,’ says there are more than 30 alloys of titanium, three of which are commonly used on jewellery:
- Grade 1: Commercially pure. Ductile; easy to form and work with hand tools.
- Grade 2: Commercially purer. Less ductile; harder, easier to machine, most available.
- Grade 5/Grade 23 6/4 ELI: An alloy of titanium with six per cent aluminum and four per cent vanadium; hard, tough, strong, available.
Common characteristics of Nb and Ti
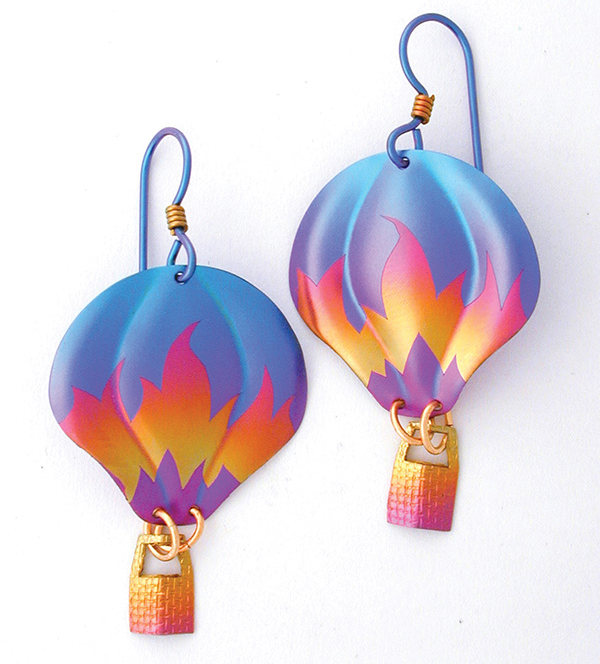
Photo courtesy Exotica Jewelry
In comparing these two metals, niobium and titanium have plenty in common. Both:
- Are hypoallergenic.
- Can be transformed into bright multiple colours using an anodizing process.
- Are very low-priced compared to palladium, platinum, and white gold.
- Resist tarnish and corrosion, and do not discolour the skin.
- Weigh less than precious metals (SG of niobium and titanium is 8.57 and 4.51, respectively, as compared to 15.58 for 18-karat yellow gold).
- Cannot be annealed in open air; must be heated in vacuum or inert atmosphere.
- Are difficult to size—niobium and titanium rings cannot be sized by the average jeweller; they must be sent to the manufacturer or sized by a specialist in the metals.
Finally, niobium and titanium are harder than gold, platinum, silver, and palladium in their pure form, according to hardness tables. Both have a hardness of 6 on the Mohs scale, though hardness values can be deceptive.
“In our experience, niobium is not as hard as gold, platinum, or palladium in their pure forms or alloys,” says Sandy Boothe of Exotica Jewelry. “Titanium in its pure form is harder than any of these metals except some of the white gold alloys. We don’t work in aircraft-grade titanium, but it is almost certainly harder than any precious metal alloys.”
Seeley agrees hardness values do not reflect the actual working characteristics of niobium. He says niobium is very slow to work harden, adding, “When you take a hammer or chasing tool to niobium, you won’t believe its hardness numbers.”
Caring for anodized metals
Jewellery with anodized niobium and titanium require special care. This is because the oxide film of such metals can easily be scratched and scraped off, which may remove the colour. Thus, anodized niobium and titanium works best for use in earrings, necklaces, pendants, and brooches; it is not as ideal for rings, which are subject to knocks. Of course, there are exceptions. When colouring is restricted to recessed areas of a titanium ring, for example, it can withstand a lifetime of wear, unlike rings with surface coloring. Niobium is seldom used by itself for rings.
The process used for anodizing metal also affects the durability of the metal oxide coating. Zoltan David, a Hungarian, Canadian, and American citizen who worked as a goldsmith and designer in Canada for 10 years, has developed proprietary techniques for creating long-lasting durable colour. An example can be seen in his fire opal, titanium, and pure gold ‘Twilight’ necklace, shown in Figure 6.
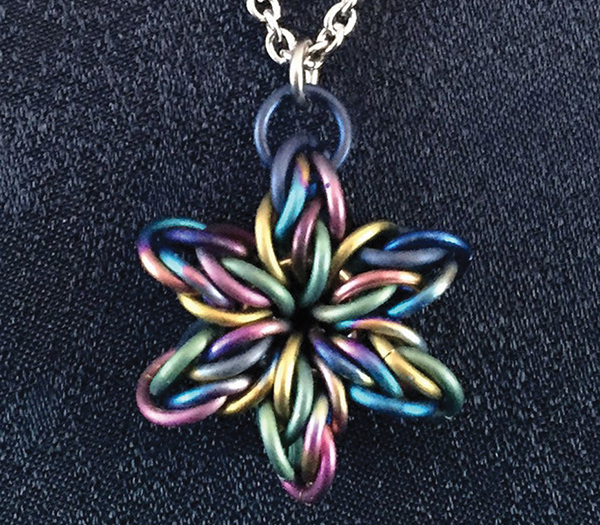
Photo courtesy Steampunk Garage
Anodized niobium and titanium can be cleaned using rubbing alcohol, Windex or a non-moisturizing mild soap, and a soft cloth. Metal polishes or abrasive soaps should not be used, as these can gradually wear away the surface colouring.
Benefits of anodization
While anodized jewellery requires special care, it also offers several advantages.
Specifically, jewellery crafted using these metals are:
1) Stable. The colour is unaffected by sunlight and does not fade. While the colour can be scratched and scraped off, it cannot peel off, as the coating is part of the metal. Aerospace companies use anodizing processes to protect metals from the effects of aging, wear, and corrosion.
2) Safe to work with (provided a jeweller wears rubber gloves). Anodizing does not involve chemicals or fumes that could be harmful to human health. Further, the coating is non-toxic.
3) Low-priced. Both the process of anodizing and the metal cost are very affordable, especially compared to precious metals. Niobium and titanium are priced by the pound or kilo instead of by the gram or troy ounce.
4) Attractive! Bright multiple colours can be achieved with anodization that are not possible with other metal colouring methods (Figure 7). Anodized niobium or titanium can be the perfect metal choice for anyone looking for striking, out-of-the-ordinary jewellery.
Renée Newman, GG, is a gemmologist and the author of Gold, Platinum, Palladium, Silver & Other Jewelry Metals and 13 other books on jewellery and gems. She became interested in jewellery metals while overseeing jewellery quality control at the Josam Diamond Corporation in downtown Los Angeles. Her metals book is used as a textbook at the Texas Institute of Jewelry Technology. For more information about Newman and her books, visit www.ReneeNewman.com.