By Chris Ploof
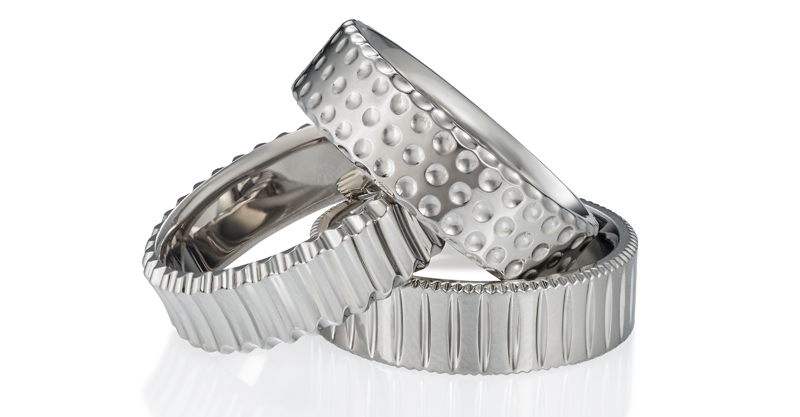
Photos courtesy Chris Ploof Designs
Modern metals are currently a “hot topic” in the world of fine jewellery, especially for bridal bands and men’s pieces. For this author, these materials have always been a fascination. I have been working with modern metals for more than 20 years now and have seen them used to make both low-quality and high-quality jewellery. I can assure you, firsthand, not all modern metals are created equal.
No doubt you have heard many claims about these metals. You may have also heard them referred to by buzzwords, like “alternative” or “contemporary” metals. For me, I am less interested in marketing and hype. The information I have comes from my direct experience of working with these materials in my studio in central Massachusetts. Direct from my jeweller’s bench, I am keen to share my knowledge, set the record straight, and demystify these metals as it relates to their use in luxury jewellery.
What follows are some of the properties that make modern metals an attractive choice for craftsman and, more importantly, for fine jewellery customers. Learning the facts about modern metals can help jewellery professionals facilitate accurate, informed conversations with clients and dispel the myriad of marketing myths that exist around these materials.
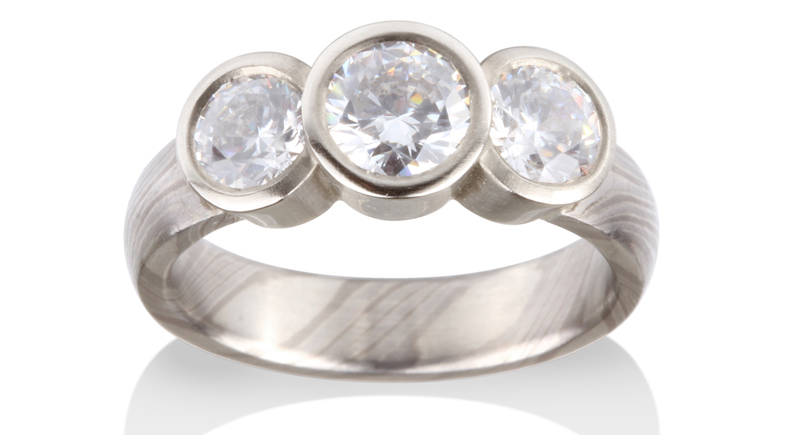
Types of modern metals
“Modern metals” is the moniker given to a group of materials that have not traditionally been used to make fine jewellery, but, today, are utilized in the crafting of items different from those seen in the “normal” precious metal category (i.e. fine silver, gold, and platinum).
Contrary to what some may say, these metals do not constitute a passing trend or fad. Rather, they are being chosen by both women and men in the contemporary marketplace for a variety of reasons. Further, when crafted properly, they can and will endure (in many cases, longer than their precious metal counterparts!).
The phrase “modern metals” comprises a broad and diverse group of materials, including steel, tungsten, titanium, cobalt chrome, Damascus steel, meteorite, tantalum, niobium, and mokume-gane, along with several very low-karat proprietary alloys. As with most things in life, not all these materials are created equal—in fact, far from it. For jewellery retailers, a little research and education can go a long way towards helping you make the right decision when buying these metals.
One good example where knowledge is critical is the case for meteorite. When choosing a jewellery supplier who deals in meteorite, it is important to be well informed and ask meaningful questions. Meteorite is an iron alloy and typically comes from a literal meteor that landed on the Earth’s surface. Not all meteorites work well for jewellery. At my studio, we dismiss more than half of the meteorite we buy as being unsuitable for use, and the remaining half may require special care to prevent corrosion. Meteorite should always be lined with a precious metal. Additionally, keep in mind that rings made with meteorite can be more difficult to size than traditional rings—arguably, though, this is a fairly small price to pay to be able to wear a 4.5-billion-year-old space metal on your finger!
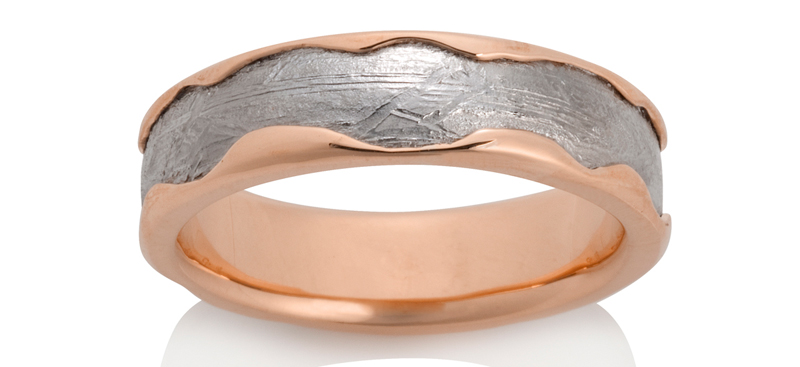
Myth No. 1: Modern metals are less durable
One common objection to modern metals is they do not endure like precious metals; however, this is not necessarily true. In fact, metals like stainless steel, titanium, and tungsten have the benefits of great strength and durability. Some suppliers are also pairing these enduring metals with precious materials, like karat gold and diamonds or gemstones. Precious metals can create a unique multi-colour look and also increase the value of jewellery. This allows retailers to earn higher margins, as the rings are elevated above a plain metal band.
If you are concerned about pieces being long-lasting, take caution with alternative materials that may seem cool at first glance but do not ultimately stand the test of time. For example, unlike the metals listed above, wood, plastic, resin, silicone, and antler do not have the durability for lifetime wear. For wedding bands especially, these are a poor choice. When wearability and sturdiness are important, opt for stainless steel, titanium, cobalt, and tungsten.
Myth No. 2: Rings or bands cannot be sized
This statement is partially true: Some modern metals, such as tungsten, cobalt, titanium, anything with plastic, stone antler, or wood inlays, can be difficult or downright impossible to size. As such, I recommend avoiding these for jewellery, especially for wedding bands. Stainless steel or plain titanium, on the other hand, are both hypoallergenic and can, in fact, be easily sized.
Beware of companies that offer “sizing,” but, in actuality, trade rings for new ones of a different size. This service feels strange and inappropriate to me, particularly for wedding rings. By trading in a band, your customer loses the physical ring they exchanged with their spouse on their wedding day, which can feel devastating.
Of course, ring sizing is often necessary throughout the lifespan—not just upon purchase, but because human beings do not typically remain the same size over time. With a durable metal that can be sized, your customer can rest assured their wedding ring can easily go up or down a size as needed over a lifetime of wear.
Tungsten and cobalt chrome are very strong and durable with a nice weight that is similar to gold. These metals are extremely difficult to scratch, but I tend to avoid them for wedding jewellery because they can be difficult or impossible to remove in an emergency and are nearly impossible to size.
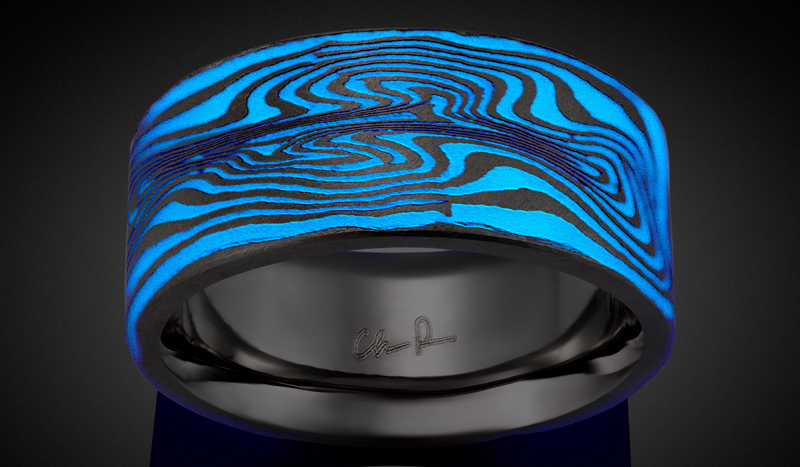
Myth No. 3: Modern metals are not environmentally sound
Some modern metals score higher than others when it comes to ethics and sustainability. Stainless steel, for example, is an economical, ethical, and environmental choice for jewellery, as it is infinitely recyclable. In fact, 60 per cent of the stainless steel on the market is recycled already before being used in jewellery. Typical grades used in jewellery are 304 and 316 austenitic steels, which, when properly worked, will not rust. I use it to make patterned Damascus steel—a metal with a rich story and one I have been working with for decades now. Not only are patterned Damascus steel pieces ethical and environmentally sound, but they are also typically sizable, easily removed in an emergency, hypoallergenic, and one-of-a-kind, given the unique snowflake or fingerprint patterning.
A word of caution regarding some Damascus steel suppliers: There are some people repurposing knife steel for jewellery, which may or may not be stainless steel. These martensitic steels can be heat treated and are great for knives, but will eventually rust, regardless of how well prepared they are.
In terms of ethics, it is important to note that some materials are officially classified as “conflict metals.” Tantalum, for example, can be sized and has a nice look, but it is officially designated as a “conflict mineral” according to the Responsible Mining Initiative (RMI) and other reliable sources. This is an example of a material not intended for, but being adapted to, jewellery use that is not an ethical choice.
Likewise, titanium has its pros and cons. While it is lightweight, durable, and recyclable, it is pulled from the earth using strip mining techniques and then refined with chlorine. These processes impose environmental threats, which is something younger consumers, in particular, care deeply about. If you choose to carry either of these metals, be prepared to be transparent about their benefits and their drawbacks.
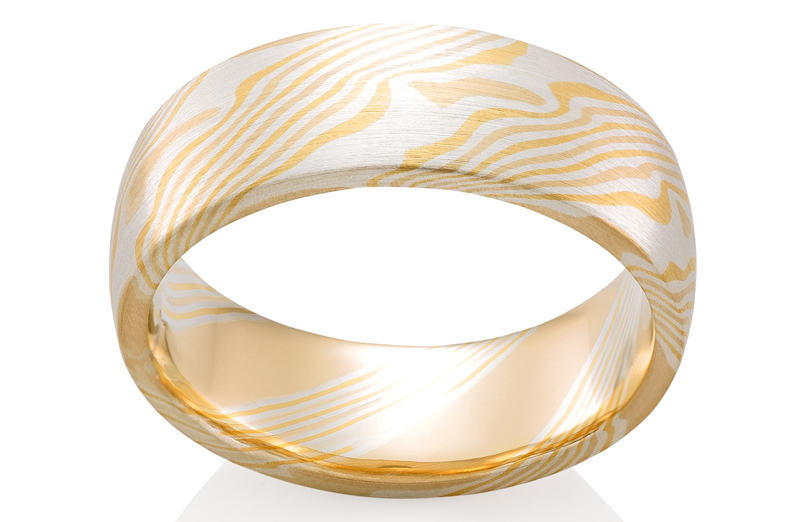
Good mythology
Metals like Damascus steel and mokume-gane require true craftsmanship, adding to their unique value. Indeed, the work each artisan puts into these materials, as well as the rich stories behind their creation and long history, enhance the value and passion clients have for their ring when they wear it.
Each modern metal comes with a deep story. Whether talking about titanium, a material prevalent in the aerospace and the high-tech world, or Damascus stainless steel, the modern equivalent of the swords of legend from the Viking Era and the Crusades, these materials have rich histories that genuinely excite consumers.
Mokume-gane is another popular modern metal that is directly linked to feudal Japan, where it was pioneered for use to make parts for samurai swords. It is crafted by way of a technique that involves laminating three or more layers of precious metal together without the use of solder, then manipulating the resulting billet using twisting, cutting, and carving techniques before creating jewellery. As a metal option for jewellery, it is a bit of an outlier, but it is a very important member of the modern metals group.
Mokume-gane used for jewellery should be made out of precious metals, as this allows for an easy introduction for customers looking for traditional materials, but also something different and unique. The technique is demanding and produces a beautiful wood-grain pattern comprised of precious metals. Mokume-gane rings can easily be sized.
The process is expensive, though (mainly because of the waste created in manufacturing). Some companies substitute copper alloys for a lower price point, but these rings will suffer from galvanic corrosion and do not stand the test of time. I recommend not using the copper alloys for commitment or bridal rings.
Stories sell
Modern metal creation and the rings made from them are backed by rich narratives. Sure, there are lots of cheap rings out there made from titanium with a CNC machine and imported from overseas, but there are also many small Canadian and American manufacturers of these unique pieces of jewellery with an equally rich story behind their company. Picking a company that is experienced with modern metals and makes the rings themselves will give you a compelling story to tell your customers and get them excited about their new ring!
Chris Ploof, an award-winning jewellery designer and metalsmith, founded Chris Ploof Designs in 2004. A specialist in modern metals, Ploof is a renowned expert in Damascus steel and Mokume Gane. His hand-forged metal jewellery designs are crafted in his solar-powered studio in Massachusetts. Ploof’s work has led to consulting projects all over the world, as well as multiple awards from the Santa Fe Symposium for his research and discoveries and countless mentions in various global trade publications.