Soldering and pickling: Tips and tricks for a smooth finish
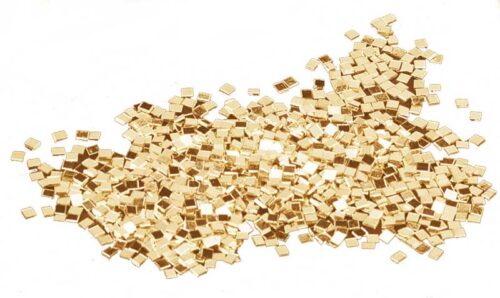
By Rafael Amador
Solder pits can be incredibly frustrating, especially during the peak season leading to the holidays. But have you ever wondered why they occur and how you could avoid them? To answer this question, here are some basic tips of the trade that you can use either during the fabrication process or while making repairs. Following these tricks should lessen your troubles, eliminate pitting, and provide your customers with quality, top-notch work.
Six measures to consider
1) Fitting: Take great care when fitting pieces to be joined. Make sure the surfaces are smooth, even, free of burrs, and fit tightly. This will ensure a strong, neat joint that requires less finishing. Remember, “solder will not fill gaps.”
2) Cleaning: Thoroughly clean all parts. The joint areas and solder must be clean, free of oxidation, oil, grease, polishing compound, and tape adhesive. If the area around the joint has a high luster, roughen the surface with a Scotch Brite pad. Also, be sure to properly dry the material as water mixing in with the solder can lead to pitting.
3) Proper support: Use clamps or jigs to align and hold the objects being soldered. Doing so will help prevent movement or shifting of the pieces during the soldering process. If the piece shifts or the alignment is off, the solder joint can potentially not adhere properly. This could lead to breakage or cause the piece to fall apart at the solder point in the future.
4) Fluxing: Using a brush, give the entire object a fire coat of boric acid and alcohol. This gently heats the object to form a protective coating, encouraging oxidation resistance. To allow for burn off during the soldering process, properly coat the joint areas with solder flux. As a liquid flux, such as Battern’s, will only provide a thin coating, more flux may need to be applied to provide the solder joint with appropriate protection. As paste fluxes are thicker, they may provide better protection on some jobs.
5) Heating: Use a slightly softer flame. Let the heat of the objects being joined flow the solder. Do not try to force the solder to flow with the torch flame as this usually results in pitting or a poor-quality joint. Apply a steady, even heat to the surrounding metal, and then concentrate the heat on the solder joint area. It is best to keep the torch moving to provide an even heat, do not overheat. It is best not to use micro torches for ring sizing as the small intense flame usually overheats or oxidizes the joint—which will undoubtably lead to pitting. Remember, “solder flows toward heat.”
6) Cleaning & pickling: Use a brush and hot water to speedily remove flux residue. Oxidation on the soldered objects can be removed in pickle solution. Hot Sparex safety pickle is the most popular pickle solution to effectively remove any surface oxides. A 10 to 20 per cent sulfuric acid solution or a 30 per cent food-grade phosphoric acid solution can also be used, although Sparex is a much safer pickle.
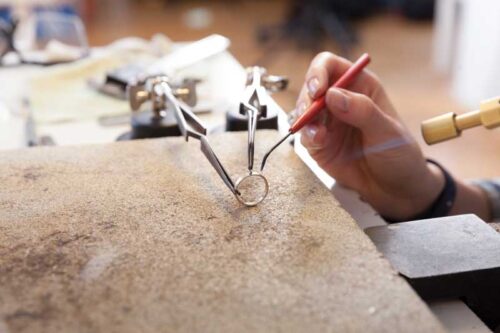
Pickle solutions
Four types of pickle solutions are commonly used to remove oxidation from gold and silver jewellery after heating or soldering. While most jewellers and professionals in the field tend to stick with just one, exploring the differences between the four may help you troubleshoot different issues in production.
1) Sparex No. 2 (sodium bi-sulfate): This is the safest and most used pickle solution for jewellery. It does not fume or cause acid burns and is safer to store than other chemicals. Although it is a bit slower than acid solutions, the sodium bi-sulfate solution removes surface oxidation very effectively. The Sparex No. 2 dry powder is mixed 1.1 kg (2.5 lbs.) per gallon of water and used hot (160-185 F in a pickle pot or crock-pot). Water should be added to the solution periodically to replace any water lost to evaporation.
2) Sulfuric acid 10-20 per cent mixed with water (always add the acid to the water): This a very effective pickle solution for jewellery. Although the solution is more effective when heated, it will fume. A somewhat lower temperature can be used to help prevent fuming. Sulfuric acid can cause acid burns, holes in clothing and damage to iron or steel tools. Rubber gloves and safety glasses are recommended when using sulfuric acid pickle.
3) Phosphoric acid (clear food-grade) 30-50 per cent mixed with water (always add the acid to the water): Although the solution is more effective when heated, it will fume. A somewhat lower temperature can be used to help prevent fuming. Phosphoric acid can cause acid burns, holes in clothing and damage to iron or steel tools. Rubber gloves and safety glasses are recommended when using phosphoric acid pickle.
4) Citric acid (food-grade): A dry powder mixed about two plus cups per gallon of water. This is an organic acid and does not fume at the usual operating temperatures or cause acid burns or holes in clothing. The solution is more effective when heated. Pickling time with citric acid will be slower than the Sparex or mineral acid pickles. Many jewellers who try citric acid and find that it is too slow often go back to using Sparex.
Another option for pickling is hydrochloric (muriatic) acid. However, it is recommended that this option be avoided when pickling gold jewellery as it can result in stress corrosion cracking.
All pickling solutions will require maintenance. Add water periodically to replace water lost to evaporation. Change the pickle solution when it becomes dirty, slows down or gets saturated with copper. Not maintaining your pickle solution could land you in a pickle of your own!
Rafael Amador is a seasoned professional of the jewellery and refining industry. He has worked with countless jewellery manufacturers within the U.S., Latin America, and the Caribbean and is a trusted expert in the field of refining precious metals. Amador joined United PMR in 2010. He currently works with United’s international team and spearheads the company’s international efforts in the region.