Evolutionary theory: A paradigm shift in technology, growth, and engagement through CAD/CAM
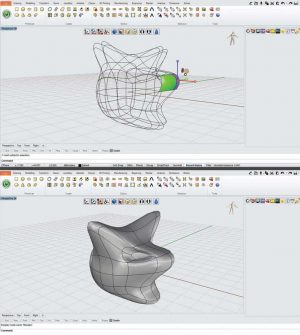
When my brother, Kamal, and I joined the CAD and 3-D printing industry seven years ago, the majority of computer-aided design software available for the jewellery industry, and in fact most others, was based on building through core features. In other words, to build a component, the user had to create the part through a series of lines (i.e. the core features). If the user wanted to build a setting, he or she created the object by tracing the claw’s path and cross section. Next, they set the software to sweep the lines, meaning, move the cross section along the path they had set. Today, most commercially available CAD software provides users with a library of ready-to-use component parts, allowing designers to spend less time building their designs. That said, core-feature software required designers possess a good understanding of building using lines, since the vast majority of objects they needed to complete a project were built in this manner.
The ability to design parametrically is a new addition to CAD design. This tool was initially developed for architects, although it has found its way into jewellery design. I was first introduced to parametric design in 2012 by one of our CAD instructors, Ralph Schroetter. Using his software, users could build CAD designs using simple logic code and varying input values. Take a cup, for example. The software allows you to break down its design features into any number of key design elements, including height, the thickness of the inside wall, degree of curve on the upper edge, and angle of flare from the bottom to the top. To build parametrically, each of those features is related to an input field, which is entered in a number box. Quite simply, the designer types in all the values regarding each of the cup’s key design features. With a couple of simple key strokes, the user can build their own cup. And so in the case of the architect, they can build a series of parametric objects, such as a door, windows, door frames, etc., by changing the input values.