Evolutionary theory: A paradigm shift in technology, growth, and engagement through CAD/CAM
Though this is a simplified example, the applications are enormous, since designers can now build parametric designs allowing them to make a wide range of objects that share similar design features. As we began introducing parametric design to our classes, we noticed students were finding new ways of reducing design time, since many features were simply a repetition of similar elements. Through parametric designing, users have found they are able to explore a wider range of organic design. The big-picture application for parametric design is the use of code to create a web-based application for e-commerce sites. Though in its infancy, this is expected to be the new way e-commerce sites will engage clients who want to participate in the creation of their jewellery.
Ahead of the curve
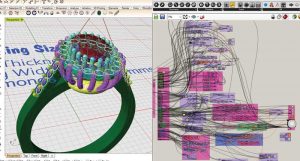
Perhaps the biggest growth we see on the horizon is the expansion of CAD software based on modular building, which provides a wide assortment of 3-D objects in a software library. We have seen first-hand through our CAD and 3-D printing academy how quickly students of varying ages can become very fluent in modular CAD design. The tool has also made its way into the jewellery industry through simplified CAD software, allowing retail sales staff to design a wide range of items using pre-designed components that can be put together on a computer screen while the clients waits. Though modular building is the quickest way to bring sales staff up to speed on CAD design, we have found users tend to find it limiting soon enough, and eventually choose to upgrade their skills by learning how to design using core features.
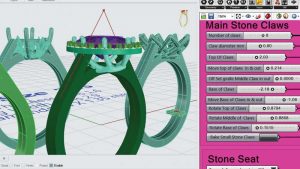
Perhaps the design style that has intrigued me the most of late is digital sculpting, which is widely used in gaming, principally in the area of building and creating characters. Though digital sculpting is starting to be used in jewellery design, it does require the user explore a completely different artistic skill set. Starting with a ‘lump of digital clay’ that has been segmented into smaller parts, the user can move, deform, reshape, and erase them to create the design. Digital sculpting does not require the designer to methodically plan out his or her object, creating instead multiple versions of their design until they achieve the desired result. Rest assured, it is usually well worth the wait.
As my brother and I explore the use of 3-D printers in other industries, we are always curious to determine how far along they are in the adoption of CAD technologies. And the answer always amazes us.
Over the last 50 years, CAD and 3-D printing technologies have been primarily a business-to-business (B2B) venture. In the last few years, Kamal and I have discovered many professionals either don’t truly know how CAD/CAM is being used within their industry or they are in the process of fully understanding the extent to which they are. Though steeped in tradition and old-world business methodologies, it is the jewellery industry, oddly enough, that has been amongst the first to convert CAD and 3-D printing from a B2B model to business-to-consumer (B2C). This push has primarily happened through the growth of various formats of CAD designing incorporated at the retail level. I guess you could say the jewellery industry is well on its way to becoming the early majority.
Hemdeep Patel is head of marketing and product development of Toronto-based Creative CADworks, a 3D CAD jewellery design and production firm. Holding a B.Sc. in physics and astronomy, Patel is a third-generation member of the jewellery industry, a graduate gemmologist, and vice-president of the Ontario chapter of the GIA alumni association. Patel can be contacted via e-mail at hemdeep@hkdlab.ca or sales@creativecadworks.ca.