All systems are go
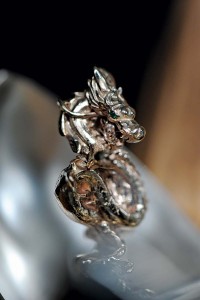
Now it was time to create the two passengers in the spaceship. I modelled the robot in CAD and scaled it to fit comfortably in its alcove. Its arms are articulated and would be milled in several pieces before assembly. The Asian dragon began as a 3D model purchased from the Internet. Since it required modifications with software I do not have, I enlisted the help of Harry Hamill, a colleague in the United States. Harry made the changes needed, such as adding five claws to each foot and giving a more sinuous twist of the tail and graceful turn of the head.
With the CAD modelling finished, I e-mailed the files to another colleague, Matthew Todhunter in Edmonton, who did a superb job of milling these complicated models. Jerome McCann, one of our goldsmiths at the time, took over the main construction. We cast the four pieces of the ship’s body, leg struts, and robot in a tarnish-resistant silver alloy, and the dragon in yellow gold. Casting larger items in silver can be problematic—one of the cabin sections failed to come out right the first time and had to be milled again and re-cast. (This is another advantage of CAD technology—it would have been very time-consuming to hand-carve a replacement.) The usual bench techniques were used to finish all the components. We had some problems during assembly due to distortion in the casting and finishing steps, as well as warping of the cabin segments, but with some tweaking, we completed the basic body of the spaceship.
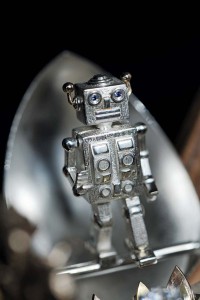
We used blue sapphire for the robot’s eyes and emerald for the dragon. The two passengers were attached to lengths of silver tubing that pivot on rods spanning the walls of the cabin segment. They can recline during ‘flight’ mode and return to a vertical position when the ship is in its open state.
The next step was to hand-fabricate the lotus blossom. We stretched the budget and decided to use three colours of gold to make three layers of petals. Circles of decreasing size were cut from thin sheets of red, yellow, and green gold and dapped to make hemispheres. These were each split into six segments and assembled in concentric layers around a central female bayonet finding using a laser welder. Initially, the flower’s centre was to be a one-carat diamond, but budgetary restraints nixed this and a cubic zirconia became the temporary replacement. The six-claw, white gold setting holding the stone has a corresponding male bayonet finding, so it can be removed and replaced with a diamond or other gem at a future date.
Final finishing and polishing came next. Since the spaceship is meant as a display piece, we decided to commission a wooden case for it. John Lavoie, a fine Calgary craftsman, created a tiger-wood egg-shape box that also opens like a three-petal flower. We fitted brass pins into the base to lock into the three exhaust jets on the base of the engine compartment. The client found a glass dome that accommodates the entire assembly, offering the couple a good dust-free environment in which to display the gift.