Going custom: A bright spot in a tough economy
The straight and narrow
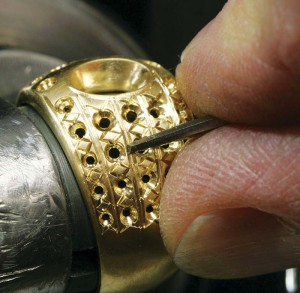
My advice is to make yourself very comfortable when cutting lines. Your arm, wrist, hand, and graver should all be in a natural straight line. I prefer cutting all the lines going in the same direction, one after the other. I then rotate the ring, get comfortable again, and cut in a new direction. Never force a cut from an unnatural position, since the graver is likely to slip and end up cutting a line across the piece. Also, remember to keep the graver razor sharp and polished, since a dull tool is likely to slip.
Sometimes the frame line does not intersect with the seat. When this happens, I use a small flat graver to remove the resulting sliver of metal. If I don’t, ugly fins of metal are created around prong beads. It is also easiest to remove them before the stones are in place.
I use a tool I call a ‘stone pusher’ to lock the diamond into its seat. Made of soft brass, it has a concave tip, much like a large beading tool. The pusher fits over the diamond’s table facet and forces the stone down into its seat. On round diamonds, I can push hard enough to actually embed the pavilion facets into the soft gold. This helps create an imprint of the stone in the metal, which in turn, keeps it tight after setting. A stone pusher is an easy tool to make. Brass can be purchased in most hobby shops or is available in jewellery tool catalogues as sprue formers. A handle from an old graver works nicely, but I prefer using one with a collet mounted on the end, which is also easily available.
Bringing it all together
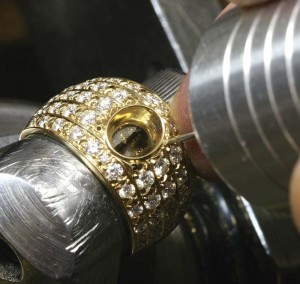
Once all 46 of the melee have been set, it is time to create the prongs for the centre stone. I have intentionally left a little bit more space above melee lines ‘two’ and ‘four’ to make room for the garnet’s prongs. This ring will not have an added crown; I want a look of unity, as though both the crown and the mounting were carved out of the same block of metal. I could have cast the prongs in place, but cast metal is not as dense or strong as pulled wire. By adding the fabricated wire for the centre crown, I am assured the prongs will be high quality.
All that is left to do is solder the prongs, set the centre stone, and do the milgraining. When possible, always solder from the inside of the ring where it is easy to clean excess flow. On the front, there should only be a neat ring of solder around the base of each prong that can be easily polished. For this project’s prongs, I used a good quality 18-karat yellow gold hard solder.
This ring was designed to have an old-fashioned look. Given its very traditional setting style, milgrain is a perfect addition to bring the whole piece together. I personally believe milgrain was originally invented to cover over mistakes, but I don’t know this for sure. I do know it has come in handy during times when my stone setting has been less than perfect. I’ve seen many bench jewellers make the error of not leaving enough space between diamonds for the milgrain tool to fit. For our example, I used a #10 milgrain tip, which needs approximately half a millimetre of space. When the seats are too close, you run the risk of the tool’s tip going over the stone and being damaged by the much harder diamonds.
Setting the centre garnet is turning out to be a simple job—this stone’s pavilion angles are close to that of a diamond. Therefore, it’s only a matter of using a regular setting bur to cut seats in the prongs. I will still take the time to check each prong and ensure there are no gaps or high points that could place uneven pressure on the stone and cause a chip. I am also careful to make sure the stone’s pavilion does not rest on the lower ring of milgrain defining the cut out. Resting a stone on a support is called ‘trapping.’ Often, the support ring will be visible through a poorly cut or windowed stone. This is one of the indicators of low-quality workmanship on the part of the stone setter.
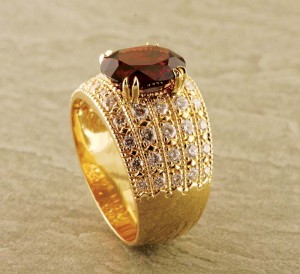
With fragile gemstones like garnet, I do as much finishing of the prongs as possible before I set. The last thing I want to do is accidentally scratch the stone with a steel file. The other benefit is that by tapering the prongs, I reduce the strength in their tips. This allows me to control the bend of the prong as it is pulled down onto the gemstone. I have accumulated many different Barrette needle files over the years. Each has been ground to a different thickness, some as thin as a business card, allowing me to work between prongs or get into other hard-to-reach places.
I was told the finished ring was a big hit. I wasn’t able to be there when it was presented to the customer, but that’s fine. As I said earlier, producing custom pieces needs to be a team effort. The important thing to keep in mind is we have to work together and not allow our individual egos get in the way of creating the perfect piece for the client.
Setting melee in this traditional four-bead style is a slow process. I can set between four and five stones per hour while maintaining a high level of quality. I estimate that by using CAD/CAM to help create the base mounting and lay out the gemstones, I saved five hours of labour. Overall, 18 hours went into creating this ring. The finished weight was 7.3 dwt. Since the ring is 13-mm wide at the top, we tapered the shank and rounded the inside edges. It was actually very comfortable to wear.
In the next issue, I’ll discuss the importance of staying current on the latest design trends and show how I made a fashionable bracelet using raw diamonds.
Tom Weishaar is a certified master bench jeweller (CMBJ) and has presented seminars on jewellery repair topics for Jewelers of America (JA). He can be contacted via e-mail at tweishaar@cox.net.