Going custom: How trend spotting can drum up custom work
Creating a raw diamond bracelet
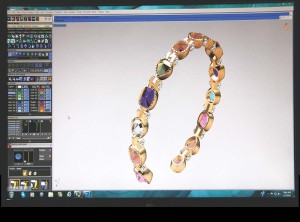
The design in the photo to the right is the fourth bracelet I have made featuring raw diamonds. I created the first three by hand, as these orders happened during the time we were transitioning to CAD/CAM. Each of the links required two to three hours of labour just to carve the wax models. This fourth bracelet was made using CAD/CAM technology, which saved about 30 hours of labour.
Adding new technology raises a philosophical question: Do we charge our customers for the time saved using CAD/CAM technology or do we pass on the savings? The answer is not as simple as you might think. Look at it this way. The customers who bought the first three bracelets each paid for 30 hours of labour, therefore, why shouldn’t the fourth? Our store spent $30,000 on CAD/CAM technology. Don’t we have the right to recoup this investment? Is it fair to charge for the labour of a machine when I can do other profitable tasks at the same time?
I believe we need to answer these questions on an individual basis. I can tell you we have chosen to pass this labour savings on to our customers. In exchange, we are hoping for a larger volume of sales in return to help pay for the technology. I don’t know if the two are linked, but here is an interesting statistic. Prior to 2012 when much of our custom work was still being done by hand, my shop produced an average of four custom pieces per month. During all of that year, we used CAD/CAM almost exclusively and produced nine custom jobs per month. We are now so busy we have decided to hire another bench jeweller and have just invested in a wax growing machine. I will discuss that technology in the next issue.
I used a wax milling machine to carve the 15 links required for our bracelet project. The six links seen in the top left photo took three hours to mill. The great part about this technology is I can focus on other tasks while the mill is doing its job. My employer loves to see the mill carving wax models while we jewellers are at our benches working. For him, it’s akin to getting two projects done for the price of one. Personally, I do miss the intimacy associated with hand-carving wax models, but when it comes to carving 15 of the same thing, the mill is very practical.
Getting richer
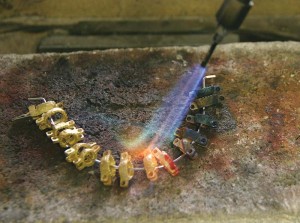
After casting the links in 18-karat yellow gold, I decided I wanted to brighten the metal so it looked more like pure gold. To do so, I strung the links on a platinum wire and heated them without using flux or deoxidizer. You can see in the photo to the left the links on the right side are now dark with oxidation. The heat has caused the copper within the alloy to congregate near the metal’s surface.
Soaking oxidized links in a 40 per cent nitric acid solution for about 20 minutes dissolves the surface layer of copper. I repeated this process a dozen times for our bracelet project. With each successive soaking, the links’ surface becomes a high-karat outer shell of near pure gold. This process is called ‘depletion gilding’ and has been used for centuries to give low-karat gold a richer appearance. On a side note: If I am ever having difficulty soldering an item, I often use an abbreviated version of this process to clean the metal. Well-cleaned metal solders much more easily than oxidized metal.
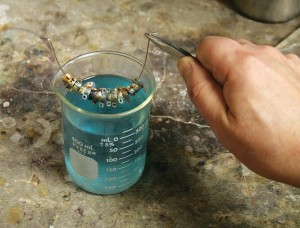
Be careful, though. Always add pure acid to water. If you make the mistake of adding water to pure acid, you are likely to get a strong chemical reaction.
As you can see from the top left photo, the links’ surface is a bright, rich golden yellow; the metal almost glows with intensity. The only problem with depletion-gilded items is the metal cannot be polished, as doing so removes the outer shell of pure gold. You can, however, burnish the item if you want a shinier appearance. Polishing is not a problem for this bracelet, since the piece will have a hammered appearance in keeping with the look of the raw diamonds.
For a full description of how I made a tongue clasp for this bracelet, see the October 2012 issue of Jewellery Business.