Adding precision to rough appearance
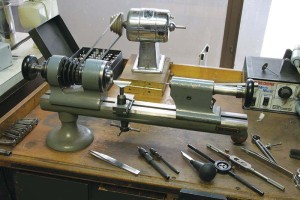
I am very fortunate my shop is well-equipped with a variety of unusual tools. One of my favourites is a circa-1940 Derbyshire watchmaker’s lathe. This piece of equipment is neither particularly rare nor is it expensive. After the Second World War, lathes like the one in the photo to the right were produced in the thousands and used by watchmakers to repair mechanical timepieces in the then-growing mechanical watch industry. Since the explosion of digital watches in the 1980s, however, lathes were no longer in demand and can now be purchased via Internet auction sites for a few hundred dollars. What makes them unusual is they are almost always regarded strictly as a watchmaker’s tool, and most bench jewellers have never been shown how to use one. With a little know-how and some practice, though, a bench jeweller can save many hours of labour and increase the quality of their work.
For our project, I used the lathe to create the threaded rivet dumbbells seen in the photo below. They will be used to connect each of the bracelet’s 15 yellow gold, raw diamond links. The rivets were designed in CAD, milled out of wax, and then cast in 18-karat white gold. The heavy main portion of the rivet is 2 mm in diameter and the threaded post is 1.2 mm. The outside end caps are each 4 mm in diameter and will be set with 1.6-mm round diamonds. All the finishing and stone-setting work was done using the watchmaker’s lathe. I’ll warn you ahead of time—stone-setting with a lathe is a lot of fun and very addictive. If you decide to invest in a lathe, you will look for ways to use it.
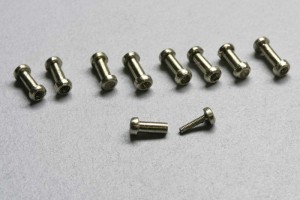
Drilling a 6-mm long hole using a standard flex shaft is very difficult work. Pressure applied to the drill bit by your hand is uneven—even a slight twist of the wrist will break the drill bit. Drilling the same hole using a lathe is a simple task. I used one bit to drill out each of the 15 rivet bodies, making them into tubes.
Once all the rivet bodies were drilled, I used a 1.2-mm tap to cut threads on the inside of the tubes. Cutting threads is a laborious task requiring great patience. Taps this small are very easy to break. In this case, I used the lathe just to align the tube and tap. Rather than turning the lathe on, I gently hand-spun the tube one turn at a time, backing the tap out and cleaning it to cut the threads. Even though I was careful, I still managed to break two taps.
Threading the rivet’s posts was a much simpler task, requiring only a 1.2-mm adjustable die and a little patience. An adjustable die has an opening on one side and three screws on the outside of the holding tool, which are used to either spread or reduce the opening of the die’s centre. With the adjustments, I was able to make threaded posts that fit snuggly into the corresponding tubes. As I assembled the bracelet, I used a small amount of Loctite on the threads to hold them in place.
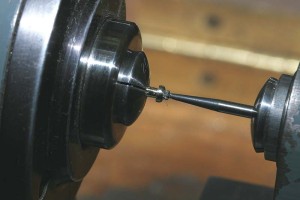
I really enjoy bezel-setting stones with a lathe. As you can see in the photo to the right, I reversed the dumbbell’s orientation so the 4-mm outer end cap is now exposed in the headstock. The lathe’s tailstock has been fitted with a 1.6-mm setting bur. Cutting a stone seat into the end cap is quick work. It’s also simple to stop and check each seat to ensure the depth on all 15 is the same.
After cutting the seats, I placed .02-carat diamonds in the end caps and burnished them in place. There is a specific tool watchmakers used to burnish jewels into watch movements, but I don’t care for it. Instead, I use a large barrette file, one side of which has been highly polished. This allows me to get a firm grip and apply strong pressure to the spinning cap. I can roll the file’s edge over the seat’s outer lip and thus roll the metal right down over the stone’s girdle. This method helps me get a very clean and uniform bezel over the stone.
After setting the stone, I use a small pointed burnisher—the same one used to flush-set stones—to push the bezel’s inside rim down onto the diamond, sealing it in place. Once the stone has been set, the entire end cap can be polished while it spins in the lathe. Setting stones with a lathe is actually a fast procedure. I can generally set between five and six stones per hour. What I like best is the uniformity of the setting work. I also use this same method to set semi-precious stones, including opals.”¨It’s great for making tube-set earrings or pendants.