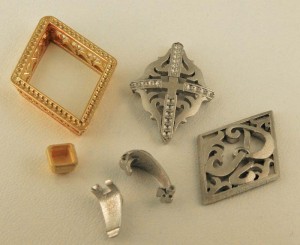
When we first investigated purchasing a 3-D printer, we heard stories about grown wax being difficult to cast. Specifically, the wax left a residue inside the flasks after burnout that could cause problems. I’m happy to report the problem has been addressed by manufacturers and grown waxes no longer leave any residue. In fact, they are as easy to cast as either carving or injection-type waxes. Note the beautifully cast pendant components in the photo to the right.
To solder the top two components, I lightly tacked the separate pieces together using a laser welder. The tacking was done from the inside, so that connection points are invisible from the front. It was also at this time that I tacked small pieces of white gold hard solder into the seam between the platinum and rose gold. The beauty of growers is the components fit so tightly together that only a speck of solder was needed to fill each seam. I always use white solder when joining white metals to other colours, as it tends to be less noticeable.
I used a different technique to solder the rear initial plate onto the back of the pendant. This time, I melted small chips of solder and flowed them onto the rim of the rose gold gallery. I used enough chips so that when the solder flowed into small pools, their edges touched each other. After quenching in pickle and cleaning in ultrasonic, I sanded the solder flat to remove any excess. This created the uniform rim of solder around the gallery’s top edge.
The process of coating a surface with solder is traditionally called tinning. The word comes from the old days when soldering was done with heavy iron rods that were heated and covered with molten tin. The tin could be kept liquid by the iron rod’s heat and then transferred to whatever needed to be soldered. Jewellers don’t use tin or iron rods for soldering, but I think the origin of our terminology is interesting.
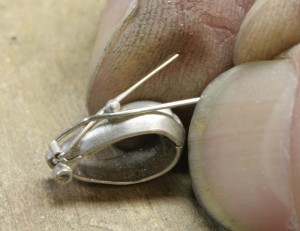
I placed the platinum initial plate over the solder and reheated everything using a large soft flame. The solder flowed a second time and was drawn up toward the hotter back plate. This process has traditionally been called ‘sweat soldering’ and was coined because jewellers gauge the heat of a piece by watching for flux to melt, pool, and then flow. Solder and flux both flow in similar temperature ranges; flux that looks like sweat is a good indicator the solder has also flowed. Be careful not to use too much flux or it will look like its crying, rather than sweating, bringing a tear to your eye when you see the messy results.
Assembling the enhancer-style bail seen in the photo to the left with its hinged rear opening, hinged pendant connection, and fold-over safety was one of the truly remarkable aspects of using the grower for this job. A platinum bail like this previously required a full day’s labour to create, along with up to a dozen soldering operations. Now with a grower, an item like this can be designed, grown, cast, and assembled in about two hours’ time.
For creating items like bails, growing machines can be a better alternative to milling operations. The bail in our pendant has many undercuts that are difficult for mills to produce. Mills also create bevelled cuts, which sometimes prevent pieces from fitting together without some additional hand finishing. For this grown bail, the pieces were lightly sanded and then snapped together. Even the hinge’s rivet pins fit snuggly in place without extra drilling. It was remarkable!