Going custom: Sign on the dotted line
Icing the cake
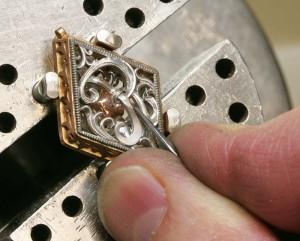
All the individual pieces in our pendant were pre-polished prior to being soldered. I think it’s very important to get as much of the heavy finishing work done before doing any surface embellishments or stone setting. I surely don’t want the hours of hand engraving to be worn down by coarse finishing work. Also, the finishing process is often the time when a pitted solder seam reveals itself. It’s best to illuminate any imperfections at this stage of the game. I want to ensure the piece is perfect before moving on to phase three of the project: hand engraving.
Hand engraving is one of my favourite things to do. I mentioned in the last issue that hand engraving became very popular about a dozen years ago. In order to keep up with my customer’s demands, I taught myself how to engrave. There are many books and several videos on the subject that helped me develop my skills. I now use air-pressure engraving tools to assist me. The photo to the right shows how I carved out the letter ‘R’ on the back of one of the pendants. I think every view of a piece of jewellery—front, side, and back—should be beautiful. I love to create items my customers will spend hours holding and discovering the small details I built into them. That’s when I feel I’ve done my job well.
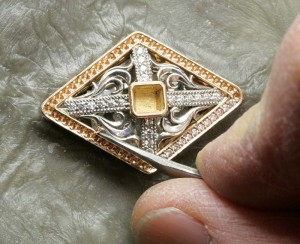
Even the front side of the enhancer bail was decorated with hand engraving. The pattern I placed on this bail is traditionally called ‘running leaf.’ My customers appreciate religious-themed jewellery, so I slightly altered the running leaf pattern to look more like two hands clasped in prayer. We also started referring to this engraving pattern as ‘praying hands.’ This one change sparked intense enthusiasm and ever since, I have created hundreds of pieces with the praying hands pattern. My best advice is to never pass up an opportunity to create imagery that speaks to your customers.
When I first began transitioning to CAD/CAM three years ago, it was tempting to quickly slam stones into seats and then move on to the next piece. At times I began to feel like I was on a jewellery assembly line and new pieces would arrive via a conveyor belt. I found it was possible to set as many as 20 stones per hour. It took some time for me to adopt a new attitude; this new technology is really only doing a portion of the rough work for me and I still need to perfect the piece by bright cutting and isolating the prongs. I now aim to set approximately eight stones per hour when using CAD/CAM.
As seen in the photo above, the pendant is mounted in plastic shellac and I’m using my onglette graver to trim excess metal from around each prong. I have previously discussed my bead- and bright-setting techniques, so I will not go into detail again. (See the February 2013 and June 2011 issues of Jewellery Business for complete discussions.) To enhance the pendant’s colour, I set the pink melee and the pink centre diamond in 18-karat rose gold. The same would be true for setting canary diamonds in yellow gold.