Going custom: The road to success
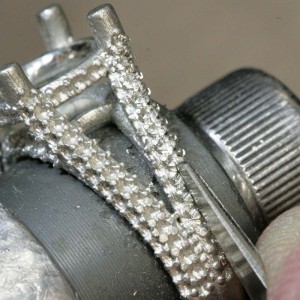
Using the graver to trim away the rough casting skin also left the prongs or beads uniform in size. This helped greatly when beading the tips, as it meant I did not have to switch out beading tools to accommodate different-size prongs.
As you can see in the photo to the right, every one of the ring’s four main legs was to be wrapped in pavé diamonds. Measuring 2 mm in diameter, each had four rows of stones. I first drilled the seats with a 0.50-mm drill bit. Since the melee is so tightly packed, I refrained from drilling all the way through the legs. This would have created azures and weakened the ring’s structure. Instead, I drilled small holes extending only a short distance into the legs.
Over the past few years, it has become very popular to place decorative cuts around prongs when setting single rows of melee. I personally like this look and have made it my practice, as well. I prefer using a very tiny onglet graver to create these scalloped cuts. Placing the graver at the centre base of the prong, I cut up and out toward the middle of each seat. I am careful not to remove any metal from the prong, as I will need it all to serve as two separate prongs.
After I’ve made all the scallop cuts and seats, I use a tiny self-made chisel to split the prong in two, right down the centre line, each half serving to set one stone. When doing this, be careful to lightly tap on the chisel with a hammer. Great care has to be taken or you might easily cut too deeply and weaken the prong.
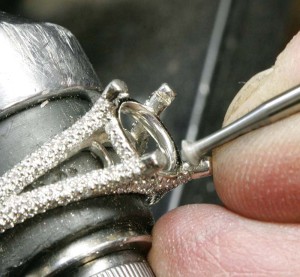
Setting work like this has to be done judiciously, as it does halve the overall size of the prongs. I personally will only do this style of setting in areas where the prongs are protected. In this case, that happened to be under the centre stone. Unfortunately, I often see this technique being used in areas where it is exposed to rough wear, resulting in stones falling out.
When pavé setting, I prefer to seat melee using a straight setting bur that is slightly smaller than the stone. The diamonds are set a bit deeper than normal, so more of the prong will be available above them to be used as tips. I then undercut with a 45-degree bearing bur. Since all the prongs on this ring are shared, I am extremely careful not to overcut them, as they will be weak and snap off.
Once a grouping of five or six stones is in place, I bead the prongs over them. A stone pusher may be necessary to ‘snap’ the melee into their seats. Properly beading prongs is extremely important and, unfortunately, many jewellers do not do a good job of it. There are more than 600 prongs tips on our ring and each one is rounded, polished, and free of snags. Your beading tool should be sized to fit snuggly and completely over the prong tip. If it is too small, it will squeeze excess metal out the sides and cause finning. On the other hand, if it is too big, it will not properly push the prong tip down onto the stones.
A beading tool can only burnish down 20 to 30 tips before it becomes rounded and worn out. I prefer using tiny carbide ball burs to reshape the beading tool’s concave tip every 20 prongs. Once the beading tip is sharp, the beader goes into the flex shaft and is spun on 1000-grit sandpaper to polish it inside and out. Notice in the photo above how clean and shiny each bead is—these tips have not been polished. (For a complete description of how to sharpen beading tools, please see Tom’s Tool Tip on page 50 of the June 2011 issue of Jewellery Business.)
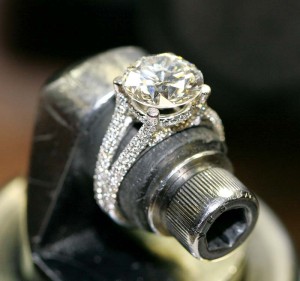
I was halfway through the process of setting the melee when our customers came by the store to check on their ring’s progress. My employer brought them into my shop and we sat for over an hour talking about how we were making the ring. I even tried to get the husband to set one of the melee, but he was too nervous. This couple was very excited about their ring and that enthusiasm is contagious. Customers who can buy an expensive ring have friends who can also afford nice jewellery. I’m sure that since this ring’s completion, the couple has been to several social events and told their friends what a great experience they had. To build your reputation and generate more custom sales, be sure to make your customers feel special by giving them excellent service and high-quality products.
Setting a four-carat high-quality diamond can be a nerve-wracking experience for any jeweller. The round diamond seen in the above photo costs much more than I can afford to replace. Even though diamonds are the hardest stone known, I treated this one as though it were a fragile emerald. As you can see in the photo, the mounting was designed so that the prongs overlapped the stone by one-third of their diameter. Those prongs are 1.8 mm wide at their tips, so I’ve got plenty of metal with which to work.
I used my favourite pair of calipers to mark where I wanted to cut seats in each prong tip. Note that marking the seats won’t ensure the cuts are perfectly level. I still prefer to place the centre stone and then hold the mounting up to the window above my bench. I’ve always felt the human eye can discern the smallest discrepancy—mine are my best level detectors.