Going custom: The rush of fabrication
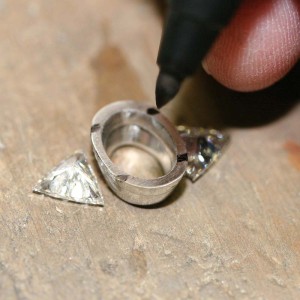
After both supports have been made, it is time to position the main prongs for the centre stone. Great care needs to be taken here. For this design, I needed to create a double-prong look between the centre oval and the side trilliants, which have a slight cushion shape so their corners fade away from the oval. To achieve that, I matched the main prong positions so they lined up with the secondary trilliant prongs.
Recently, a young bench jeweller asked me if there was a ratio between prong diameter and the size of the stone they are holding. The answer I gave is, “Yes, and I wish I knew what it was.” I was not trying to be flippant with my remark, as it is obvious we use larger prongs to hold bigger diamonds. It’s just that there is no accepted standard for this ratio. I normally use 0.80 mm (20 ga.) diameter for stones up to .75 carats, 1 mm (18 ga.) for stones up to 1.50 carats, and 1.25 mm (16 ga.) for stones more than 1.50 carats. I also like to use wide, though thin prongs, that I split for stones with corners, such as cushion cuts.
In the photo below, I am using a Kraus bur to cut grooves in the gallery supports for the prongs. This procedure creates a lap joint. I do not like the appearance of prongs simply butted up and soldered to the outside of the supports. Butt joints require more solder and are not as strong as lap joints.
Soldering platinum items together used to be very difficult due to the high heat required. Since metal tools could not be used to hold the parts, jewellers would carve all sorts of niches into ceramic blocks to hold them together while the first few solder joints were being made. That all changed with the invention of the laser welder. This tool is perfect for lightly tacking parts together in inconspicuous places before soldering the units. The laser makes it possible to create multiple solder joints at one time. I also like to tack small pieces of solder into the inside seam between two parts and then use a torch to pull the solder to the outside. This method practically ensures a pit-free solder joint.
Phase two—side crowns
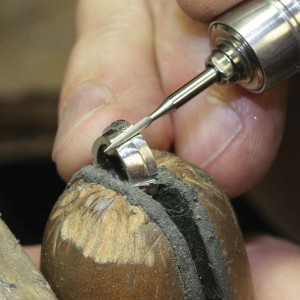
With the centre crown now complete, it’s time to turn our attention to the crowns for the trilliant diamonds. I prefer to use a ‘cut and fold’ method for making supports that come to points, such as a triangle, square, marquise, or pear. This requires a very accurate measuring of the stones. Next, I deduct approximately 10 per cent from the stone size so the supports will be smaller than the stones. The new measurement is then transferred to my stock, which was 1.5 mm x 1 mm. My goal is to create two triangular supports that won’t be visible when viewing the ring from above.
I used a saw to cut a groove halfway through the metal, followed by a square file to open a V-notch in the groove. As the metal was folded, I reused both the file and the saw blade to carefully remove metal from the notch until the stock folded together in the tight seam. It is necessary to anneal the metal several times during the folding process. Just as in sizing a ring, it is important not to have gaps in the seams if you want to avoid pitted solder joints. I used ‘1700’ platinum solder for the two upper gallery supports after folding them tightly.
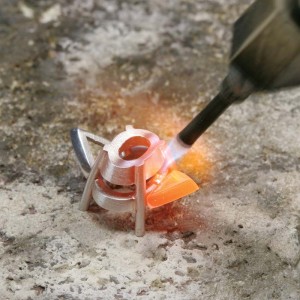
We can see in the photo to the right that the three-stone ring is starting to take shape. These side crowns were soldered in place using ‘1600’ platinum solder. Note how every surface is either polished or sanded to a 1000-grit finish. This is the ultimate beauty of a hand-fabricated piece of jewellery. Each section can be finished prior to assembly, allowing you to end up with a flawless look.
When setting stones with points like trilliants, I prefer to use chevron prongs where possible. I believe this type of prong offers the greatest protection for fragile tips. I also think they look better than standard round wires. I made the chevron prongs for this ring by taking 2-mm square stock and cutting a flat side on one half. Next, I used a 90 degree Hart bur to cut a groove down the length on the now triangular stock. This grooved piece of metal was then cut into two pieces, mitered into the ring, and soldered in place.