Going custom: The rush of fabrication
Phase three—making the shank
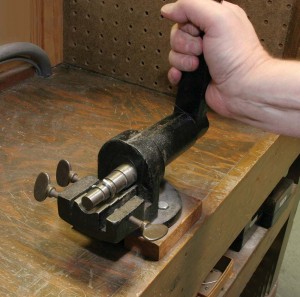
To create the ring’s shank, I began with a 2-in. length of 3-mm square stock. This is actually too thick for the shank’s lower portion, but I needed the thickness for the upper section. I marked the metal and then used the rolling mill to reduce the thickness in the middle. As a rule, I like ring shanks to be less than 2-mm on the back side and between the fingers. Thick ring shanks are heavy, expensive, and uncomfortable to wear.
The antique tool seen in the photo to the right is called a shank bender. It has an off-set cam that allows you to insert a metal blank; a quick tug on the handle rotates the mandrel into the corresponding form, bending the metal into a ring shank. The same can be achieved with shank-bending pliers, but the shank bender is easier on the hands and does not dent the metal. Heavy-duty cast iron versions of this tool are no longer in production, but they do occasionally appear on Internet auction sites. They are a great buy if you can get one for under $100.
Partway through fabrication, I decided to change the shank’s design. If you look at the original drawing, you can see the shank is heavy in appearance. Since the ring design has traditional upper and lower gallery supports with a space between them, I decided to carry this element through to the shank. I slit the metal with a saw and used a prong lifter to elevate the shank’s upper leg. Visually, this will lighten the look of the shank. Once all the rough shaping of the shank was complete, I filed it, sanded it to a1000-grit finish, and in some spots, polished it to its final form. I prefer to ensure everything is perfect before final soldering.
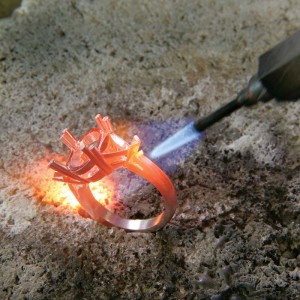
I’d like to use this final project to discuss soldering platinum. Firstly, all the images of soldering in this article were taken when the metal was still relatively cold, otherwise I would have needed a dark filter on the camera. Platinum solders flow in the range of 1600 C to 1700 C, or roughly 3000 F. Jewellers need to wear number ’10’ (or higher) welding goggles to protect their eyes from the ultraviolet light emitted by the glowing metal.
Also, do not use flux or fire coating when soldering platinum; it is a pure metal that does not oxidize during soldering, so no coatings are necessary. Flux—which we know melts in the same temperature range as gold solders—is absorbed into platinum at high heat and can break down the bonds between the grain boundaries.
This ring was constructed using a combination of ‘1600’ to ‘1700’ platinum solders. Unlike gold or silver, platinum dissipates heat very quickly, which means you can solder very close to a previous seam and not be overly concerned with melting it. I tried to show how this ring was assembled using lap joints with good surface contact, rather than weaker butt joints. The amount of surface contact helps keep everything together during soldering.
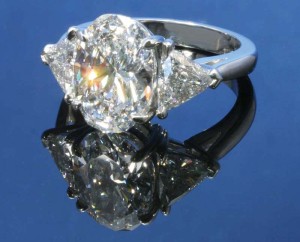
Platinum solders of 1500 C or lower are alloyed with palladium to bring down the melting temperature. I only use these solders (and never less than ‘1400’) when attaching lightweight platinum filigree into heavier mountings.
I think the platinum three-stone ring turned out well. The customer loved it and that’s what really matters. This job took a total of 16 hours to complete, including all stone setting. Fabricating this ring was a rare pleasure for me. It’s been a long time since I didn’t have to turn a computer on to make a ring.
As this is my last article, I want to thank my editor, Jacquie De Almeida, and all the wonderful staff at Jewellery Business for allowing me to be a part of the magazine for the past five years. I also want to thank the many readers who e-mailed questions and comments. Thank you all for your support.
Tom Weishaar is a certified master bench jeweller (CMBJ) and has presented seminars on jewellery repair topics for Jewelers of America (JA). He is an award-winning columnist, picking up Silver at the Kenneth R. Wilson awards for his six-part series on stone-setting techniques.