Is it time to add manufacturing technology to your store?
Shifting gears
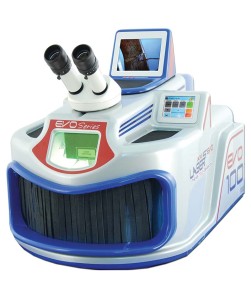
There’s also the potential for new business opportunities. Camgozlu notes that with a laser welder, jewellers can do work that wouldn’t be possible with a torch, such as fixing eye glasses.
Even repairs that are possible with traditional methods take a fraction of the time with a laser welder, says Daniel Kundakci at European Design Jewellery.
“The laser welder more than pays off the initial investment,” he says. “The time and money saved… is incredible.”
John Tufenkjian, president of Sassounian Montreal, says most jewellers looking to buy an entry-level rapid prototype machine are making anywhere from three to five custom pieces a week. With service bureaus charging up to $150 for each job, a $24,000 machine can pay for itself in about a year.
Although the interest is there, Tufenkjian says, jewellers of all ages seem to resist technology, preferring instead to do things old-school. It’s a mindset he says he encounters all the time. He is quick to point out, however, those who embrace the techie side to making jewellery are likely building their businesses at a faster pace.
“Nowadays, when you’re in neutral, you may be actually going in reverse,” he adds.
For any retailer, the ability to control their own repairs and save the cost of outsourcing is a major plus, says Kundakci. It’s also more efficient, allowing a retailer to take on more jobs and pay off the machine. He uses the example of re-tipping a claw with heat-sensitive stones, which can take an hour or more with a torch, but just two minutes with a laser welder. A retailer can also weld all types of metals, including titanium and steel, Kundakci adds.
Putting in the time and effort
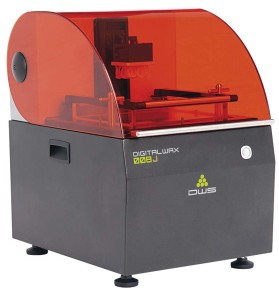
Yet, even proponents of manufacturing technology acknowledge incorporating machinery and software into a business can be a challenge. “The learning curve is quite steep,” says DaCosta. “It’s not something you can just sit down and do instinctively. It takes some time.”
However, nearly all machine technology companies offer extensive training and say it’s a skill that can be mastered with practice. “Any goldsmith can learn how to use a laser welder,” says Kundakci. “The transition is a lot easier than what some goldsmiths may be concerned about.”
Most operators can be trained in one to two days, he says, adding the company ensures a customer is comfortable before stepping back.
NS CNC Manufacturing in Vancouver also offers training for its milling machines. Jennifer Robinson, director of business development and planning, says if a client has already learned to use 3-D drafting software, “it gives them an edge.”
For a jeweller who is technically savvy, training can be easy, she adds, noting most don’t need to hire extra staff to work the equipment.
“It is unusual for us to sell a five-axis mill to an experienced jeweller who still makes models by hand,” explains Robinson. “Most of our clients are somewhat experienced, at least in design, so it makes using the technology easier.”
However, all agree that when it comes to new technology, the longer a jeweller spends learning the intricacies of a program and working on designs, the better the outcome.
“The learning curve is a little bit different for each person,” says Plunkett, explaining ArtCam usually takes two to three days to train a client on its software. However, it can be a challenge for some craftspeople to adjust to dealing with a 3-D design on a monitor.
“Humans are creatures of habit,” explains Plunkett. “Some people are used to working with their hands—it’s just learning and adapting.”
Nicole MacIntyre is a journalist and freelance writer based in Burlington, Ont. She has covered breaking news, politics, and lifestyle issues for nearly a decade. MacIntyre has received multiple nominations and awards for her work, including an Ontario Newspaper Award.