Mastering the method of manufacture
A case for casting
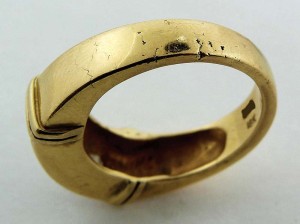
Note the telltale signs of cracking and pitting.
Casting is one of the oldest known methods for making jewellery and has been around for thousands of years in various forms. Very simply, it involves a process that creates one or multiple items without having to make each one from scratch. The most prevalent method—lost-wax casting—involves making a model from an organic material like wax or resin, either carved by hand or machine, and more recently, grown with a 3-D printer. The model is packed into investment and dissolved by heat to form a negative void. Molten metal is then injected under some form of centrifugal or vacuum force, pulling it into the cavity. Ages past, goldsmiths used to sling the mould around by hand, kind of like David whirling his slingshot at Goliath (but of course, not letting go).
Lots of things can go wrong with casting, but the good news is, mistakes leave traces. On occasion, the only clue one might have that an item was most likely cast is the piece itself. It would have been almost impossible to create a true 3-D piece of jewellery any other way.
All qualities of jewellery can be cast, so you might see the ridiculous (e.g. an inexpensive diamond tennis bracelet with imperfect diamonds cast in place) to the sublime (e.g. a Cartier brooch). In most cases, antique platinum pieces, especially filigree, are not cast. Generally speaking, cast pieces appear heavier and bulky. Upon closer inspection, though, you might find the piece is a reproduction. At the turn of the century, Edmond Fouch of France developed the first oxy-acetylene torch, which produced a very hot flame, far hotter than any gas flame before it. With this new tool, and given platinum’s ductile strength, craftsmen were able to create delicate pierced pieces, which were almost always hand-fabricated. It’s not until recent times that we see any quantity of cast platinum pieces; most of what you will see is bridal jewellery.
What to look for in a cast piece:
- Porosity ranges from microscopic to large pinholes and can be caused by trapped gasses or when the metal is not heated or cooled properly. Metal that cools too quickly can also result in cracking. Porosity can go deep into a casting and sometimes is not revealed until the final polishing process.
- Lack of joint/solder marks, which can be a sign of a one-piece casting.
- Seam marks on the inside of castings made from rubber moulds.
- Even when a piece appears to be made of two colours of metal, the item can still be a one-piece casting; the top prong work holding any diamonds might have been rhodium-plated to make the piece appear more labour-intensive.
- The 3-D nature of the piece would not lend itself to the use of other techniques, such as die-striking or hand-fabrication.
- A slightly matte ‘skin’ on the underside and inside holes or crevices of a design.1 In addition, the matte skin can have the appearance of moiré silk, a sure sign the wax mould was made using CAD/CAM, which implies it’s not ‘antique.’
Jewellery can be one-piece cast or assembled of various cast, hand-made, and pre-fabricated components.
What to look for in an assembled piece:
- Visible solder joins between components.
- Porosity in the solder joining the components.
- Identical mould lines from the original wax design. This is pretty good evidence a piece has been cast and assembled, especially when it’s a bracelet. One would see an identical line or imperfection repeated inside each cast link.
- Noticeable differences in polish between the two metals
(e.g. platinum top with a yellow gold base).