Meeting Cullinan: A jewellery appraiser’s unofficial guide to the famous diamond mine
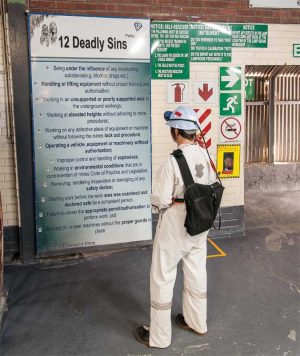
While en route to the shaft, we’re told about new near-infrared spectroscopy and x-ray transmission imaging technology being used to mitigate damage of large valuable crystals. These developments are especially important for a mine such as the Cullinan, a source frequently yielding diamonds larger than 10 carats. The mine has produced more than 800 stones weighing over 100 carats, 140 stones weighing over 200 carats, and approximately a quarter of all diamonds mined weighing over 400 carats. In addition, Cullinan is the only reliable source for very rare and valuable blue diamonds. A new plant nearing completion has been built with the future in mind; this facility will continue to use and improve these modern tools.
The descent
Underground mining is the next step in extracting diamond-bearing rock once opened pits have become too steep, unsafe, or too expensive to work in.
We arrive at the cage, the only way in and out of the mine, and take the 2.5-minute long ear-popping ride underground alongside a full complement of working miners. When the heavy steel doors slide up and out of the way, a tired and dusty crew is waiting to go back up—miners work in shifts; 2 a.m. to 10 a.m., 10 a.m. to 6 p.m., and 7 p.m. to 2 a.m. As the miners with whom we rode disperse into different tunnels, we stay near our guide so we don’t get lost.
Inside Cullinan
To assuage those readers who might be a bit claustrophobic, once at the bottom, the mine feels surprisingly spacious, despite its rough walls and dim lighting. A thick layer of dust covers everything; the tunnels are lined with unused trolley tracks and there is ample room to accommodate large trucks and heavy equipment. Overhead, I can trace the colour-coded pipes bringing water and fresh air in, and the pipes clearing out carbon monoxide. In these tunnels, there are offices, break-rooms and refuge spaces, which are marked by amber light and easily found in the dark or emergency conditions.
Gone are the days of jamming sticks of dynamite into rock seams and running for cover. A clear non-volatile gel is mixed with another chemical and soon the mixture turns a thick, opaque blue. A carefully monitored electrical charge will activate this explosive.
We walk the tunnels, hewn of solid bedrock supporting the work to extract and push along the unstable kimberlite for processing. Once broken or blasted away, the kimberlite is dumped into ground-level chutes that funnel the rock to the two huge ore elevators. The elevators bring the diamond-bearing rock up to the surface where the process of crushing, washing, and sorting begins. Some of these older chutes, as well as much larger pieces of equipment, are rusty and decommissioned, but it isn’t cost effective to dismantle and remove them from the mine.

Around these transfer points, we pick up and examine pieces of the kimberlite, also known as blue ground. The dark sandy rock is damp and crumbly, with shiny bits of chromite catching the light of our headlamps.
A memorable experience
The cage ride up to ground-level is silent; perhaps we’re all glad to be above ground, or maybe struck silent with a sense of admiration for the men and women working in the mines.
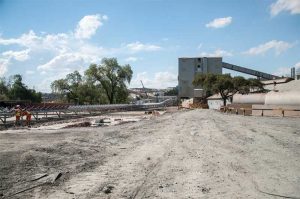
We trek to see the view of Cullinan’s big hole, then return to the tourist centre and walk through the showroom where visitors can buy trademarked Cullinan Star Cut faceted diamonds. This proprietary cut is a round brilliant diamond with 66 facets. A certificate of provenance accompanies these goods as verification the diamond was mined here and can only be purchased at Cullinan Diamonds.