Multiple deadlines: A jeweller’s nightmare
New technology to the rescue
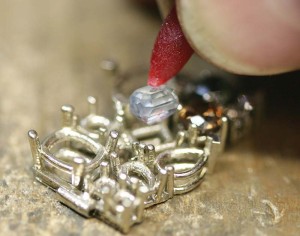
My second concern was even worse. Milling machines are great for most design projects. They are fast and inexpensive to operate, but they can have difficulties cutting out recesses or hidden spaces. My design called for creating seven multi-basket-style sections. These would each have many hidden areas that our mill could not reach. I tried several times to come up with a method to mill the first necklace section. I decided to divide the section into an upper and a lower segment. My plan was to join the two sections together and then cast it as a single unit. I even went so far as to cast a practice model, but the results were poor. A new solution was needed.
The store’s management team had been discussing the possibility of purchasing a 3-D wax printer (also known as a grower) for the past year. This particular design helped cement our decision—we ordered the machine.
Don’t you love getting new stuff?
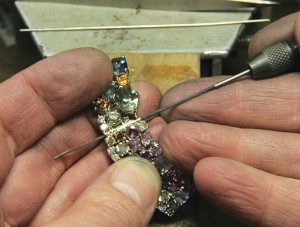
While the 3-D printer was being shipped, I used the time to work on the CAD designs for the necklace’s other six sections. The grower arrived in late November and I was only finished with five of the seven sections. Projects were coming into the store quickly, and I could not devote all my time to just the necklace. The machine was quickly tested and then immediately put to task growing the waxes for different projects. During the first three days, everything went well with the printer, but problems arose on day four. The manufacturer ran remote tests on the machine via the Internet for several days. Ultimately, a technician was flown out to access our situation. Heat was the problem. We had placed the grower in a south-facing room that had a big window. During the day, the sun beat down directly onto the grower, throwing off the machine’s temperature calibrations and ruining its sensitive printer heads.
This could have been a sad story, but the manufacturer was fabulous. We returned the old machine, while a new one was in transit—time was the only cost to us. When the new grower arrived, it was moved to a much cooler section of the building and I am now very careful about monitoring its temperature settings. Since then, the grower has worked flawlessly.
Assembling and setting
You can see in the opposite bottom photo the grower did a great job of creating the individual sections. They each cast perfectly and fit together like seven gloves. At this point, I mistakenly thought I had cleared all the big hurdles in creating this project. My only problem now seemed to be time. The delay with the grower had cost me more than a week’s time, however, I was able to complete other projects in the queue. With a clear calendar before me, it was time to start setting the sapphires.