Risky business
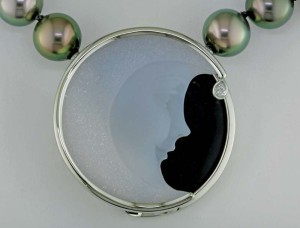
Erkki Mursula, one of our goldsmiths, began by making two fully circular bezels in white gold plate approximately 0.8 mm thick, high enough to encompass the full depth of the carvings, plus a few extra millimetres. Next, with the carving held in place, he used a sharp scribe to trace the contours of the stones’ front on the inside of each bezel, leaving the back the full height for the time being. Following this line, Erkki trimmed the excess metal from the front of the bezel.
For the bezel’s front, he used a circle made from very well annealed white gold rectangular wire measuring approximately 2.0 x 0.7 mm. This was malleable enough to be manipulated to conform to the contours of the top of the bezel. Working around the perimeter, Erkki tacked the wire to the bezel with the laser welder. Once done, he soldered the pieces together, and filed and shaped the resultant bezel rim.
With the fronts attached on both bezels, it was time to fit white gold bearings behind the carvings to support them in their bezels. Using a similar technique, the bearings (this time approximately 2.0- x 2.0-mm square wire) were first tacked to secure the carvings in place. Of course, with the carvings in the bezels, soldering was not possible, so Erkki used the laser welder with fill wire to completely attach the bearings with no risk to the gems. Once filed and finished, the joint was invisible and the carvings were set securely.
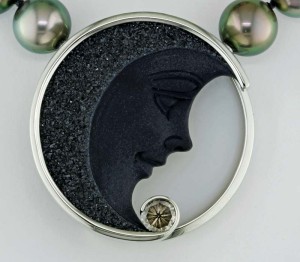
The piece was to be reversible with the two carvings attached back to back. This meant the rear surface of each carving would be visible and provide a contrasting backdrop to the carving facing forward. Erkki removed the unnecessary segments of the circular bezels once he had welded supporting metal at the tips of each crescent. This served to isolate and enhance the arc of each moon.
The next step was to attach the bezel-set carvings together. The pendant was to include a proprietary clasp, which meant we had to fit the male bayonet cylinders between the two carvings. To accommodate the carvings’ undulating contours, we used white gold plate to bridge the variable gaps between the backs of the bezels and laser-welded them. Next, we drilled holes in the bridges to accommodate the bayonet findings. Three points of connection were adequate and we oriented them such that the two at the top attached to a chain or pearl strand and the third, located at the bottom, could hold an optional pearl or gemstone accent drop.
To complete the piece, I chose a 0.09-carat pear-shape white diamond that was bezel-set and attached (with an articulated connection) to the upper tip of the white agate crescent moon. On the black side, I used an odd-ball round diamond that had been in inventory for many years. It is a 1.02-carat fancy round-cut by Gabi Tolkowsky and is yellowish-grey in colour with rather a lot of internal inclusions. Under a loupe, the clusters of black specks are concentrated in a crescent shape on one edge of the diamond, providing a subtle and secret re-enforcement of the pendant’s theme.
The client who ultimately purchased the pendant already had several pieces of jewellery that use the same clasp system, meaning she can wear it with several of her existing pearl strands, as well as a stainless steel chain or even a black silicone neck cord.