The realm of possibility: Managing clients’ CAD expectations
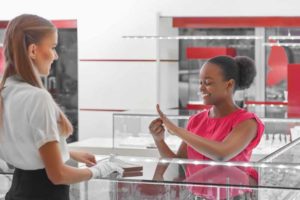
A realistic picture
Perhaps the biggest pitfall is retailers are distracted by the infinite possibilities of design without knowing the realistic limitations of CAD and 3D printing. By understanding these limiting factors, retailers can better appreciate what types of designs can be delivered, what kind of timeframe they should be looking at, and—most importantly—whether it is even possible to design, print, and finish the piece.
One of these limiting factors is the skill level of the CAD designer. With the ever-growing number of design styles now exploding in the jewellery industry, the CAD designer’s abilities can affect what retailers are able to bring to market. Further, these designers are just starting to broaden their skills to address the growing trend of jewellery pieces inspired by organic designs. Each piece can be considered a form of digital art, where the required skills and timeframes are unheard of compared to designing most jewellery pieces. These pieces require additional skills such as using organic modelling software tools, and can take days, if not weeks, to design, rather than the mere hours needed to create most non-organic pieces.
The next limitation is the sheer computing power of the system being used to run the CAD software. At its simplest, this software is a series of 1s and 0s. Each element designed is a unique group of 1s and 0s, and the more elements you have, the more groups there are. Thus, every time the designer needs to move, manipulate, or alter an element, the software needs to run a new set of computations with all the 1s and 0s.
Eventually, every computer system will hit its computational limits. This normally happens when designs have more than 500 different elements, ranging from claws and stones to CAD-related design tools like cutters. In this instance, computer will either slow right down, rendering the use of a keyboard and mouse useless, or shut down the software entirely.
A significant constraint lies in what designs can be 3D printed and eventually cast into precious metal. Though it is possible to design virtually anything with CAD software, natural limitations are tied to the capabilities of the 3D printer and the available casting techniques. Though some high-precision printers are capable of printing to a dimensional width of 0.05 mm (0.001 in.), features designed at this size will not survive the casting and polishing process, since the initial polish can quickly cause a deviation of 0.1 mm (0.003 in.).
In the case of hand-applied features like milgraining, which can be quite labour intensive, it can be tempting to take a shortcut by just designing the beads on CAD and printing them directly onto the model. However, when the milgrained model is cast and polished, there will be an obvious difference compared to a hand-milgrained edge. The hand-applied version will always leave behind a sharp and bright milgrained finish that cannot be duplicated by a 3D printer.
As with any new venture or service offering, there is always a learning curve involved in CAD, but with an open line of communication between your client and CAD designer, these challenges can be managed and overcome. It is also vital retailers begin to educate themselves on the strengths and weaknesses of CAD and 3D printing in order to better understand the potential growth and limitations of this emerging technology.
Hemdeep Patel has been writing since 2008 on a variety of topics relating to the jewellery industry, from advanced gemmology, gemstone, and diamond trends to emerging jewellery CAD/CAM technologies. He is head of business strategy and marketing for Creative CADworks, a 3D CAD/CAM firm specializing in design, production, and 3D printer and resin sales. He is a third-generation member of the jewellery industry. Currently, Patel is vice-president of the Gemological Institute of America (GIA) Alumni Association for the Ontario Chapter. He is a graduate gemmologist and holds a B.Sc. in physics and astronomy. He can be contacted via e-mail at hemdeep@creativecadworks.ca.