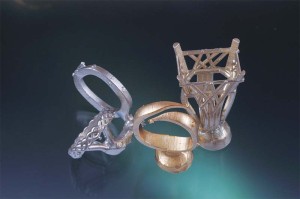
In my own work, comprised mostly of custom design, I try to embrace the idea of sole-authorship when possible. As such, I can relate to the desire to maintain direct involvement in each step it takes to make one of my custom pieces. This seems to be a subjective decision and one each designer must make for themselves.
The element of time it takes in finishing a project, however, may be more objective and affected by both the location of your business and the nature of your work. Master goldsmith Dino Giannetti of Toronto’s 18Karat, says he chooses not to cast his projects. “I can drop off my carved waxes or grown designs one day and pick them up the next here in downtown Toronto.” Giannetti also makes a good point when he mentions the variety of metals with which he works and how that affects his decision. He may need several castings in any given production cycle, “With one of them being 14-karat yellow gold, one 18-karat yellow gold, one 14-karat rose gold, and several platinum, does it make any sense for me to maintain a separate system for each of these metals? For me, it makes more sense to let the experts in each of these metals do the work for me.”
One could also point out not all metals are easily castable with less-than-optimal equipment. It is one thing to cast gold alloys and quite another to cast palladium, for example. Casting most gold alloys can be accomplished to a high degree of success with a torch, kiln, and spring-loaded centrifuge. Palladium, however, requires induction melt, inert cover gas, and a vacuum-assisted centrifuge to cast successfully. In this case, even if you routinely cast gold in your shop, you will likely send out palladium castings to a trade shop set up for the process.