A matter of time
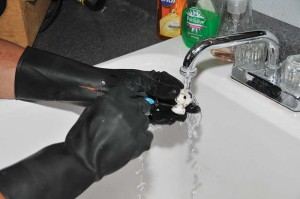
Casting involves many steps: spruing, investing, burnout (which requires venting), and actual casting, each either needing separate space or involving a cleanup and set-up routine whenever the process is implemented. Time involved in the constant space shuffle can become overbearing if one considers it a form of currency. A good argument can be made that it is much easier to track an expense if you pay cash for it. That is, it may be easier to track and control overhead when one is laying out capital, rather than personal time on a project. My own experience confirms personal time tends to get overlooked in the overhead equation.
Tom Wright of Wright’s Jewelers in Lincoln, Neb., has “pointed views” on the topic of casting, as he puts it. “I do most of my casting in-shop because I primarily want to offer unusual or different things in my work,” he says. “I have no intent to re-invent the wheel and I use carving and casting to set myself apart from the competition, to make my shop special.” Therefore, he usually casts most objects as single castings. At first during our conversation, he mentioned casting gave him a “competitive edge,” but after a brief pause, he adjusted that thought to, “By carving and casting, I don’t really have to compete, since you can’t buy my designs anywhere else in the world.” He does send casting out, however, when he has a production situation. One example of this occurred in a recent Christmas season when he was asked to produce 50 of one item. After casting the original, he sent out the remainder of the production to free up his time for other projects.